Special delivery
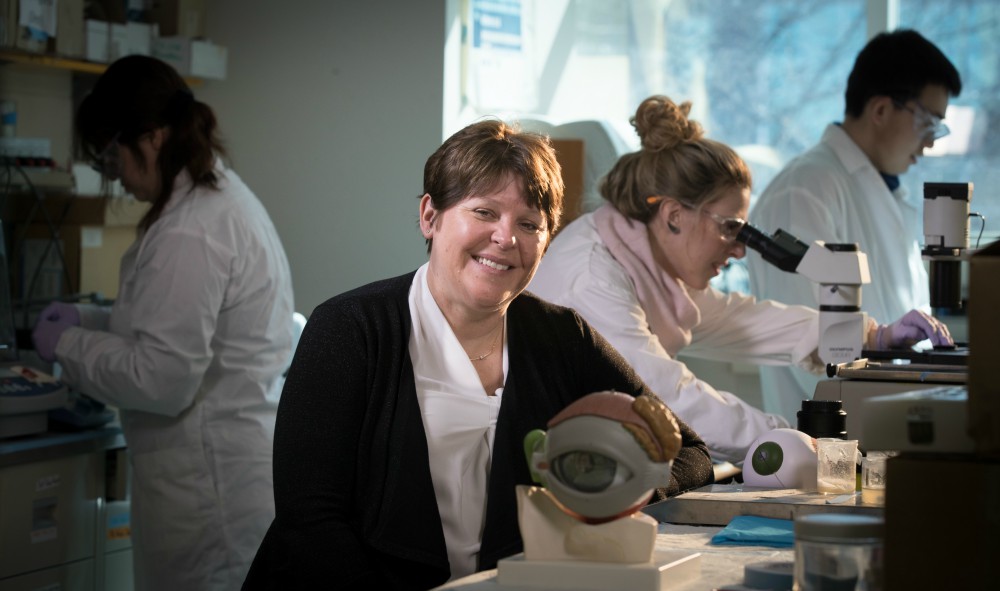
March 6, 2018
Tears are an amazing feat of natural engineering. Made up of three distinct layers, they keep the cornea – the “skin” of the eye – hydrated and protected against bacteria, and provide a smooth, clear surface to look through.
Tears work well. In fact, they work a little too well if you’re using old-school eyedrops to get medicine into your eye. Swept away by your all-too-efficient tears down your throat and across your cheeks, up to 95 per cent of the drop won’t actually make it to the target tissues.
This means eyedrops need to be reapplied regularly, often in concentrations that can sting – and it means they aren’t as effective they could be.
For Heather Sheardown, the solution to outsmarting eyes’ natural engineering was, naturally, more engineering.
The chemical engineering professor and Canada Research Chair in Ophthalmic Biomaterials and Drug Delivery has developed a way to deliver microscopic “packets” of medicine inside micelles, sphere-shaped fatty molecules that stick to the eye’s mucous layer. This stickiness prevents micelles from being washed away by tears and allows them to release drugs over time – so eyedrops that once had to be administered every day can now be used just once a week.
Sheardown and her team have started a company, 20/20 OptimEyes, to bring this technology to market, initially targeting dry eye disease, a common condition caused when eyes don’t produce enough tears.
“Cyclosporine A, which is currently used to treat dry eye, is carried in a horrible formulation,” explains Sheardown. “It stings going on, and because you’re getting such a small amount of medication to the eye, you have to use it for a long time before you feel any effects. Although we’re targeting dry eye for now, the system is amenable to lots of other types of drugs, like glaucoma medications, antibiotics and anti-inflammatories.”
Sheardown will now have the support of the brand-new Fraunhofer Project Centre for Biomedical Engineering and Advanced Manufacturing (BEAM), opening March 7, as she and her team explore the path to commercializing technologies developed in their lab.
A partnership between McMaster and the Fraunhofer Institute for Cell Therapy and Immunology, a European leader in cell therapy manufacturing, BEAM will focus on applied biomedical research in four key business areas: cell and gene therapies, drugs, diagnostics, and biosystems technology.
For researchers like Sheardown, who is one of BEAM’s directors, the centre will bridge the gap between industry and the work being done in academic labs, giving labs advanced facilities to do the scale-up pre-clinical testing and manufacturing to prove to industry that a technology is robust enough for commercialization.
Sheardown expects BEAM will make a huge difference in translating lab work into health-related products. “We’re working on getting things into the hands of physicians or patients where they can be used to improve quality of life,” says Sheardown. “It’s exciting.”